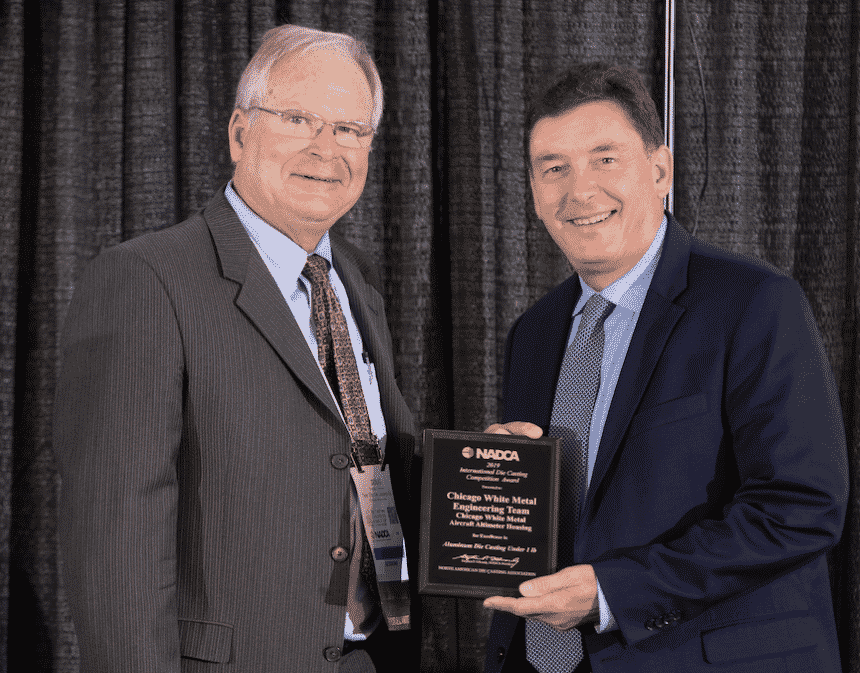
CWM and Aerosonic Take Flight with NADCA Award
Congratulations to the Chicago White Metal Casting and Aerosonic Engineering teams for winning yet another North American Die Casting Association (NADCA) award for design excellence in 2019! The NADCA Award for Design Excellence is a prestigious die cast engineering award which enlists a committee chosen