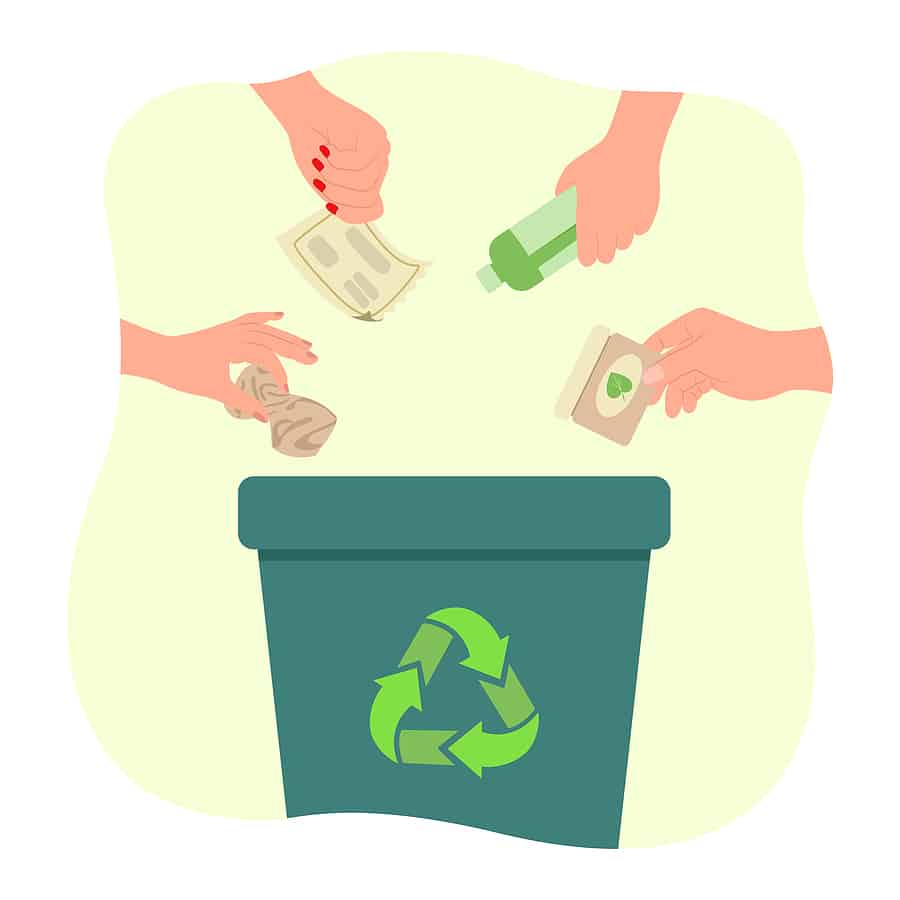
CWM Recycling Stats – September 2023
In September 2023, CWM recycled the following to Imperial Recycling: In addition to that, our partner Groot picked up nearly 5 yards of mixed recyclables. That included 479 pounds of cans, plastic bottles, newspapers, etc., deposited in our blue barrels around the facility. In September,